ADEV埃登威氧化鋯氧分析儀**氧化鋯氧分析技術(shù)的*新進(jìn)展
電化學(xué)傳感器氣體分析技術(shù)在控制能源和原料消耗、改善工業(yè)過程生產(chǎn)率以及控制污染物排放等工業(yè)領(lǐng)域,正在發(fā)揮日益重要的作用。事實(shí)上,汽車工業(yè)早已開發(fā)出各種固態(tài)傳感器,用于汽車發(fā)電機(jī)燃燒效率控制。目前,**于汽車工業(yè)的這項(xiàng)檢測(cè)技術(shù)已將應(yīng)用領(lǐng)域拓展至工業(yè)窯爐、鍋爐和汽輪機(jī)等 。
如今,氧化鋯氧量傳感器廣泛應(yīng)用于各種工業(yè)領(lǐng)域和運(yùn)輸工具。上世紀(jì)70年代初期,在鋼鐵生產(chǎn)控制中**采用了一次性氧化鋯氧量傳感器,分析鐵水中的氧含量。上世紀(jì)60年代,為了開發(fā)固態(tài)氧燃料電池(SOFC),研制出堅(jiān)固耐用的鉑電極和固態(tài)氧化鋯電解質(zhì)(氧化鋯結(jié)晶體)。其后,美國西屋電氣公司在此基礎(chǔ)上,開發(fā)出**臺(tái)用于過程氣體分析的工業(yè)用氧化鋯氧量傳感器。時(shí)至今日,氧化鋯氧量傳感器的主要應(yīng)用仍然集中在控制汽車發(fā)動(dòng)機(jī)的空氣/燃油比
在空氣與燃油混合點(diǎn)火時(shí),要求空氣要達(dá)到一定的比例,以期使燃燒過程完全充分。燃燒后廢氣中的氧含量可以直接反映燃料混合物中空氣量的相對(duì)富?;蛳鄬?duì)不足。自上世紀(jì)70年代起,氧化鋯氧量傳感器,或稱為λ傳感器,一直用于監(jiān)視汽車廢氣中的氧含量。
在空氣與燃油混合點(diǎn)火時(shí),要求空氣要達(dá)到一定的比例,以期使燃燒過程完全充分。燃燒后廢氣中的氧含量可以直接反映燃料混合物中空氣量的相對(duì)富?;蛳鄬?duì)不足。自上世紀(jì)70年代起,氧化鋯氧量傳感器,或稱為λ傳感器,一直用于監(jiān)視汽車廢氣中的氧含量。
1976年,受普通火花賽設(shè)計(jì)的影響,德國博世公司**在其不加熱的錐管型λ傳感器(LS)中,裝入了氧化鋯傳感器本體,用于汽車發(fā)動(dòng)機(jī)的反饋燃油控制。不加熱的氧化鋯氧量傳感器僅僅依靠廢氣的熱量,使工作溫度達(dá)到600-900℃。
1982年,德國博世研制了**代加熱的錐管型λ傳感器(LSH),目的是減少冷啟動(dòng)時(shí)的廢氣排放。
1997年,德國博世又開發(fā)了加熱的平面型λ傳感器(LSF)。LSF傳感器由鉑電極、固態(tài)氧化鋯電解質(zhì)(氧化鋯結(jié)晶)、絕緣材料和加熱器組成,采用分層結(jié)構(gòu),疊壓在薄形基片上。
*新型的氧化鋯傳感器技術(shù)是基于平面型λ傳感器設(shè)計(jì),具有直接測(cè)量空氣/燃油比的功能。以往所有的λ氧傳感器均采用傳統(tǒng)的來回切換式設(shè)計(jì)。*新的寬帶式λ傳感器(WB)則完全摒棄了這種設(shè)計(jì)理念,可以產(chǎn)生與空氣/燃油比成正比的信號(hào)。
寬帶式氧化鋯傳感器與錐管型或平面型傳感器的相同之處在于:當(dāng)空氣/燃料比中的空氣量相對(duì)不足時(shí),產(chǎn)生一個(gè)低電壓信號(hào);當(dāng)空氣量相對(duì)富裕時(shí),產(chǎn)生一個(gè)高電壓信號(hào)。不同之處在于:寬帶式氧化鋯傳感器沒有快速的切換動(dòng)作,而是根據(jù)空氣/燃料比中空氣量的相對(duì)富?;蛳鄬?duì)不足,緩慢地增加或減少電壓。在*佳空氣/燃料控制比14.7:1位置,寬帶式氧化鋯傳感器會(huì)產(chǎn)生穩(wěn)定的450mV電壓信號(hào)。若空氣量出現(xiàn)微小的相對(duì)富裕或相對(duì)不足時(shí),傳感器的輸出電壓也相應(yīng)地產(chǎn)生微小變化,而不是劇烈地增加或減少。寬帶式氧化鋯傳感器的另一個(gè)不同之處在于加熱器電路。與平面型傳感器一樣,寬帶氧化鋯傳感器的加熱器電路也是印制在陶瓷片上,但是采用脈沖持續(xù)時(shí)間模塊化設(shè)計(jì),使工作溫度穩(wěn)定在700-800℃范圍內(nèi)。BOSCH的寬帶式λ傳感器,即LSU 4.9,對(duì)空氣/燃油混合物變化的響應(yīng)時(shí)間小于0.1秒,其內(nèi)部加熱器可以使傳感器的工作溫度在20秒內(nèi)達(dá)到800℃。
氧氣泵是寬帶式氧化鋯傳感器的組成部分。為了**測(cè)量,氧氣泵抽取被測(cè)排放氣體,注入到電化學(xué)電池組(稱為能斯特電池)之間的“擴(kuò)散”間隙。能斯特電池用導(dǎo)線與氧氣泵連接,根據(jù)“擴(kuò)散”間隙中的氧含量,能斯特電池分流一部分電流。當(dāng)電流值達(dá)到動(dòng)態(tài)平衡時(shí),其與被測(cè)排放氣體中的氧含量成正比,該信號(hào)可以為發(fā)動(dòng)機(jī)的計(jì)算裝置,提供**的空氣/燃油比,從而滿足國際*新的汽車排放標(biāo)準(zhǔn)。
氧化鋯傳感器開發(fā)的另一個(gè)重要里程碑,是由意大利ADEV埃登威率先引入了焙燒鉑金屬陶瓷電極技術(shù)和釉底料技術(shù)。所謂的釉底料技術(shù)是將多孔保護(hù)膜與等離子噴涂晶體層技術(shù)相結(jié)合,形成雙保護(hù)層系統(tǒng) 盡管用于汽車工業(yè)排放控制的λ傳感器非常先進(jìn)、可靠,但還是很難適應(yīng)在線工業(yè)過程的應(yīng)用要求,問題的主要癥結(jié)在于嚴(yán)酷的工作環(huán)境和傳感器的封裝材料。
2. 理論基礎(chǔ)
所有工業(yè)用氧化鋯傳感器均基于以下原理:電池由固態(tài)氧化鋯電解質(zhì)(絕大部分為穩(wěn)定的氧化釔?氧化鋯,簡(jiǎn)稱YSZ)和兩個(gè)鉑電極所組成。鉑電極焙燒在氧化鋯陶瓷片的兩側(cè),暴露在被測(cè)過程氣和參比氣中:
O2(參比側(cè)氧分壓),鉑電極 │ 氧化鋯 │鉑電極,O2(測(cè)量側(cè)氧分壓)
使用高溫密封材料和氧化鋯陶瓷片,使測(cè)量側(cè)與參比側(cè)徹底分離。由于氧化鋯傳感器兩側(cè)的氧濃度不同,形成濃差電勢(shì)E,該電勢(shì)大小符合能斯特方程: 式中,
C為常數(shù),與氧化鋯鋯頭的熱接點(diǎn)、參比側(cè)與測(cè)量側(cè)的溫度和壓差有關(guān);R為通用氣體常數(shù);T為被測(cè)過程氣的溫度,單位K;F為法拉第常數(shù)。
氧反應(yīng)發(fā)生在“三相區(qū)域”(簡(jiǎn)稱TPB,即鉑電極、固態(tài)氧化鋯電解質(zhì)和被測(cè)氣體),其中, O2代表氧分子;e’代表電子;VO”代表氧離子空穴(請(qǐng)參閱圖1A)。氧反應(yīng)過程包括:氧分子吸收、電解質(zhì)/電極表面分解、以及*后擴(kuò)散至TPB,在TPB處發(fā)生氧電化學(xué)反應(yīng)。如果使用復(fù)合的離子-電子導(dǎo)電電極,或者帶電子和離子導(dǎo)體的陶瓷電極(例如:鉑-氧化鋯),則在電極主體發(fā)生氧電化學(xué)反應(yīng),這樣可以有效改善氧傳感器的使用性能(請(qǐng)參閱圖1B)。
O2(氧氣)? O2(電解質(zhì) / 電極)
O2(電解質(zhì) / 電極)? 2O(電解質(zhì) / 電極)
2O(電解質(zhì) / 電極)? 2O(電解質(zhì) / 電極 / 被測(cè)氣體)
2O(TPB)+ 4e’(電極)+ 2VO”(電解質(zhì))? OO(電解質(zhì))
圖1. 氧傳感器電化學(xué)反應(yīng)
通常,在參比側(cè)固定氧分壓,例如,空氣壓力p(O2)=0.21bar時(shí),熱平衡型氧傳感器上的信號(hào)只取決于過程和/或傳感器加熱器溫度。
工業(yè)氧化鋯氧量傳感器通常工作在300℃以上的溫度條件下,氧離子在氧化鋯傳感器中遷移,并*終在氧化鋯的測(cè)量側(cè)、參比側(cè)和氧化鋯電解質(zhì)表界面實(shí)現(xiàn)氧平衡。提高工作溫
度可以改善傳感器的性能,但是,高溫對(duì)傳感器的封裝材料是一個(gè)極大的挑戰(zhàn)。因此,絕大多數(shù)工業(yè)用氧化鋯氧量傳感器的工作溫度在700-800℃范圍內(nèi)。
3. 氧化鋯鋯頭設(shè)計(jì)
工業(yè)用氧化鋯氧量傳感器的有兩種設(shè)計(jì)結(jié)構(gòu),一種是密閉的鋯管結(jié)構(gòu),另一種是將盤狀鋯池封裝在鋁質(zhì)或其它金屬鋯管上的結(jié)構(gòu)(參閱圖3)。
圖3. 氧化鋯鋯池示意圖
鋯管結(jié)構(gòu)或“套筒式”工業(yè)設(shè)計(jì),具有良好的使用性能,但是,由于鋯池陶瓷組件帶凸緣結(jié)構(gòu),形狀較為復(fù)雜,且整個(gè)鋯管均受到熱應(yīng)力的影響,因此,該氧化鋯鋯池的強(qiáng)度較差。此外,鋯池中的電化學(xué)反應(yīng)區(qū)域的熱平衡也不能達(dá)到*佳狀態(tài)。
盤狀鋯池封裝在金屬鋯管上的結(jié)構(gòu),由于金屬盤和金屬鋯管的熱膨脹系數(shù)完全匹配,因此,參比側(cè)與測(cè)量側(cè)之間的溫差很小,氧化鋯陶瓷組件所受的熱應(yīng)力影響也很少。此外,獨(dú)特的多孔鉑-氧化鋯陶瓷電極組件設(shè)計(jì),拓寬了發(fā)生氧反應(yīng)的TPB界面,改善了氧傳感器的響應(yīng)時(shí)間和使用壽命。
工業(yè)用氧傳感器的*高品質(zhì)規(guī)格是工業(yè)在線應(yīng)用,即要求氧化鋯氧量傳感器即使是在極端溫度和爆炸性環(huán)境,也能可靠地工作多年(請(qǐng)參閱圖6-7)。
圖6. ZR202G氧分析儀(日本橫河)
圖7. X-STREAM 氧分析儀(Rosemount Analytical)
Inconel、哈氏合金或316L不銹鋼屬于特種合金,在高溫過程環(huán)境條件下,具有優(yōu)異的抗氧化和抗腐蝕性能。可以使用上述合金制做氧化鋯鋯管、內(nèi)部標(biāo)定氣管線和參比氣管線(請(qǐng)參閱圖8)。
圖8. X-STREAM O2氧化鋯鋯頭組件
特制的氧化鋯鋯池組件可以改善熱平衡,陶瓷或金屬擴(kuò)散元件適用于含高粉塵的測(cè)量應(yīng)用。這兩個(gè)特性均可以提高氧分析儀的性能(請(qǐng)參閱圖9)。
4.用氧化鋯分析儀監(jiān)控燃燒過程
工業(yè)用氧化鋯分析儀廣泛用于燃燒過程的監(jiān)測(cè)與控制,應(yīng)用范圍包括耗能行業(yè)(鋼鐵、電力、石油化工、陶瓷工藝、紙漿造紙、食品、紡織)和各種燃燒設(shè)備(鍋爐或焚化爐等)。*佳的燃燒狀態(tài)要求煙氣中CO2含量應(yīng)達(dá)到*大值,O2濃度則應(yīng)接近于零。
在*佳燃燒狀態(tài),氧氣和燃料的配比應(yīng)符合理想比例。通常,煙氣中的主要成分是二氧化碳CO2和水H2O。此外,還有極少量的其它氣體,如二氧化硫SO2和氮氧化物NOX,這些氣體來自于燃料雜質(zhì)和空氣中的氮?dú)獗谎趸?
理想的化學(xué)計(jì)量點(diǎn)——*高效率和*低排放,在實(shí)際燃燒過程中是無法實(shí)現(xiàn)的,原因是燃料/空氣的配比、燃能密度、燃料和空氣流量都不是一成不變的。氧化燃燒過程會(huì)造成熱量損耗,并產(chǎn)生大量的氮氧化物污染;還原燃燒過程燃燒不完全的燃料,通過煙囪會(huì)排放大量煤煙,造成環(huán)境污染,同時(shí)極大地縮短燃燒器的使用壽命。此外,由于燃料、空氣不可能完全混合,因此,理想燃燒實(shí)際上是不可能實(shí)現(xiàn)的,絕大多數(shù)燃燒設(shè)備煙氣氧含量均控制在幾個(gè)百分點(diǎn)。通常,燃?xì)馊紵鳠煔庋鹾靠刂圃?-3%;鍋爐和燃油燃燒器煙氣氧含量控制在為2-6%。煙氣溫度越低,燃燒效率越高。
一般來說,氧含量控制在0.75-2%,燃燒可達(dá)到*佳狀態(tài)。不同的煙氣溫度,燃燒過程氧含量每減少1%,可節(jié)約燃料1-3%。
與燃?xì)?或燃油鍋爐不同,燃煤鍋爐的煙氣含有大量粉塵,如:飛灰、硫和二氧化硫SO2等。眾所周知,抽取式的分析系統(tǒng)存在堵塞和冷凝問題,與之相比,直插式O2/CO測(cè)量技術(shù)就顯示出較高的可靠性。
單獨(dú)測(cè)量煙氣的氧含量可以較好地控制燃燒過程,如果同時(shí)再測(cè)量一氧化碳CO,則可以進(jìn)一步提高燃燒效率和控制穩(wěn)定性。經(jīng)驗(yàn)證明:若煙氣中含有約100ppm的一氧化碳和少量的氧,則燃燒過程可以接近化學(xué)計(jì)量點(diǎn),達(dá)到*高的燃燒效率。燃煤電廠鍋爐平均的O2/CO濃度測(cè)量示例
用氧化鋯分析儀監(jiān)測(cè)氧和一氧化碳,控制燃燒過程,對(duì)降低氮氧化物NOX和二氧化硫SO2排放也是有效的。因?yàn)橥瑫r(shí)監(jiān)測(cè)兩個(gè)參數(shù),可以控制燃料燃燒更完全,使燃燒過程接近于化學(xué)計(jì)量點(diǎn),燃燒效率*高,此時(shí)氧含量控制在1-2%。
燃燒過程中,煙氣溫度是變量,氧化鋯分析儀可以在檢測(cè)氧含量的同時(shí),觀測(cè)到煙氣溫度的變化。在煙氣溫度變化過程中,為了使氧含量測(cè)量更準(zhǔn)確,信號(hào)更穩(wěn)定,要求氧
化鋯分析儀要能夠保持熱平衡,以消除熱接點(diǎn)對(duì)氧測(cè)量信號(hào)的影響(市場(chǎng)上有些氧化鋯分析儀,溫度的波動(dòng)影響達(dá)到10mV,對(duì)氧測(cè)量信號(hào)的影響為3±1%O2)。
煙氣溫度變化對(duì)Rosemount Analytical的X-STREAM氧化鋯分析儀的斜率和常數(shù)影響極小當(dāng)被測(cè)過程溫度在25-600℃范圍內(nèi)變化時(shí),由此產(chǎn)生的氧含量測(cè)量誤差小于±0.025%O2(請(qǐng)參閱圖14)。這一新型的工業(yè)用氧化鋯分析儀可以在較寬測(cè)量范圍內(nèi),保證氧含量測(cè)量的穩(wěn)定性和**度。但是,不包括在空氣中測(cè)量,因?yàn)榭諝鉂穸鹊淖兓瘯?huì)影響氧分壓,而傳感器的測(cè)量信號(hào)與氧濃度成對(duì)數(shù)關(guān)系,因而會(huì)給傳感器引入比較可觀的測(cè)量誤差
實(shí)時(shí)控制可以有效地改善現(xiàn)代燃燒控制過程。一般情況下,燃燒控制過程可以分成兩類:操作點(diǎn)控制(OPC)和有效燃燒控制(ACC)。
在有效燃燒控制ACC中,控制器的輸出用于調(diào)節(jié)流量特性,例如調(diào)節(jié)燃料流量。ACC已經(jīng)在許多分層火焰燃燒爐和紊流燃燒器中取得了不同程度的業(yè)績(jī)。貧燃料預(yù)混燃燒可以降低火焰溫度,因而是減低NOX排放的有效方法。但是,這種方法有兩個(gè)缺點(diǎn),一是熄火,二是控制穩(wěn)定性不好 [2]。在這種控制應(yīng)用中,要求氧化鋯傳感器必須能夠迅速、**地確定燃燒系統(tǒng)的工作狀況。燃燒不穩(wěn)定的情況是經(jīng)常發(fā)生的,其發(fā)生頻率小于500Hz,故在這種控制應(yīng)用中,要求傳感器的實(shí)時(shí)響應(yīng)頻率要達(dá)到kHz級(jí),這樣才能提供有效的反饋控制信號(hào)。
操作點(diǎn)控制(OPC)是通過調(diào)節(jié)燃料注入量,控制火焰參數(shù)。這種控制沒有**的空氣流量信息,只是基于實(shí)際的火焰特性和估計(jì)的空氣流量進(jìn)行控制。在這種控制應(yīng)用中,可以利用氧化鋯傳感器的測(cè)量結(jié)果,**地調(diào)節(jié)燃料/空氣比。
有關(guān)氧化鋯氧量傳感器的材質(zhì)、在不同環(huán)境中傳感器的使用性能和應(yīng)用限制等更多詳細(xì)信息,可以參閱*近發(fā)表的相關(guān)資料。
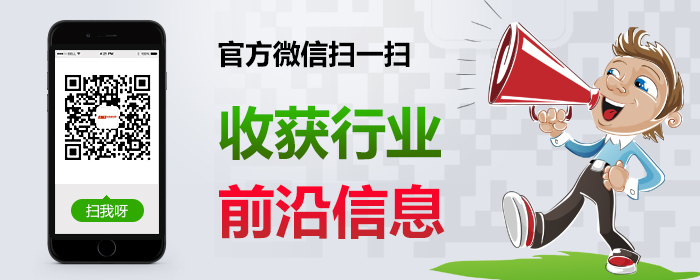